As you all know, the FDA FSMA 204 compliance deadline of January 20, 2026, is approaching, and the food industry must prepare for the extensive recordkeeping and traceability requirements. FSMA 204, part of the FDA’s broader Food Safety Modernization Act (FSMA), demands a higher level of transparency and accuracy in the food supply chain, particularly for those dealing in high-risk foods.
This article explores distributors’ specific challenges, provides actionable insights, and highlights best practices to achieve compliance without disrupting operations.
1. Why It Matters for Food Distributors
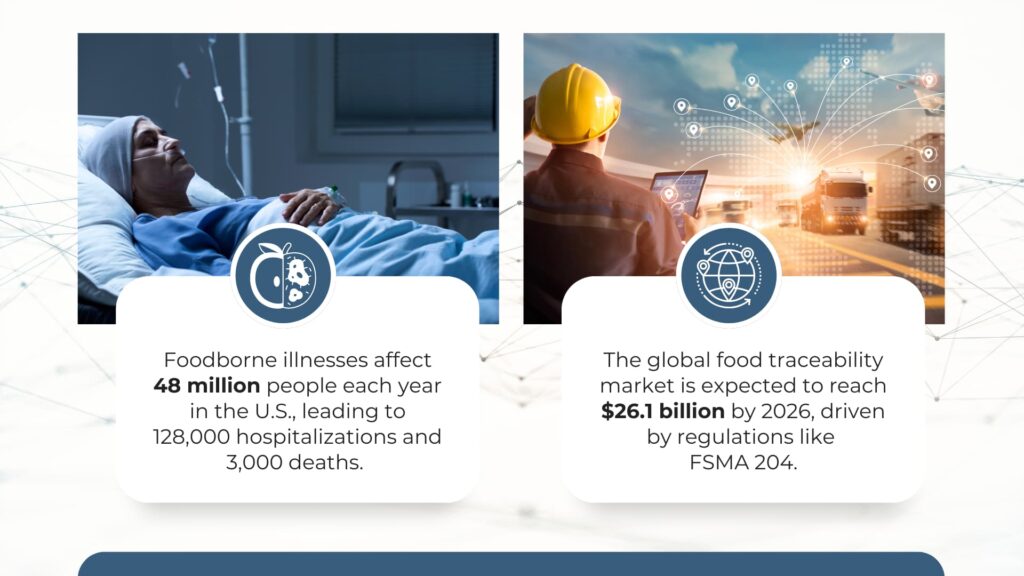
The FSMA 204 rule mandates stringent recordkeeping and traceability for high-risk foods, including seafood, soft & semi-soft cheeses, shell eggs, nut butters, ready-to-eat deli salads and fresh produce. Distributors of these foods must maintain detailed records of their receipt, storage and shipment, ensuring the ability to quickly trace any product in case of contamination.
Consider a food distributor handling seafood, categorized as high-risk under FSMA 204. Without an advanced traceability system, a recall could take days, leading to widespread contamination and a significant loss in consumer trust. However, with a comprehensive traceability solution, the source of contamination can be identified within hours, drastically reducing the scope and impact of the recall.
2. The Unique Challenges Faced by Food Distributors
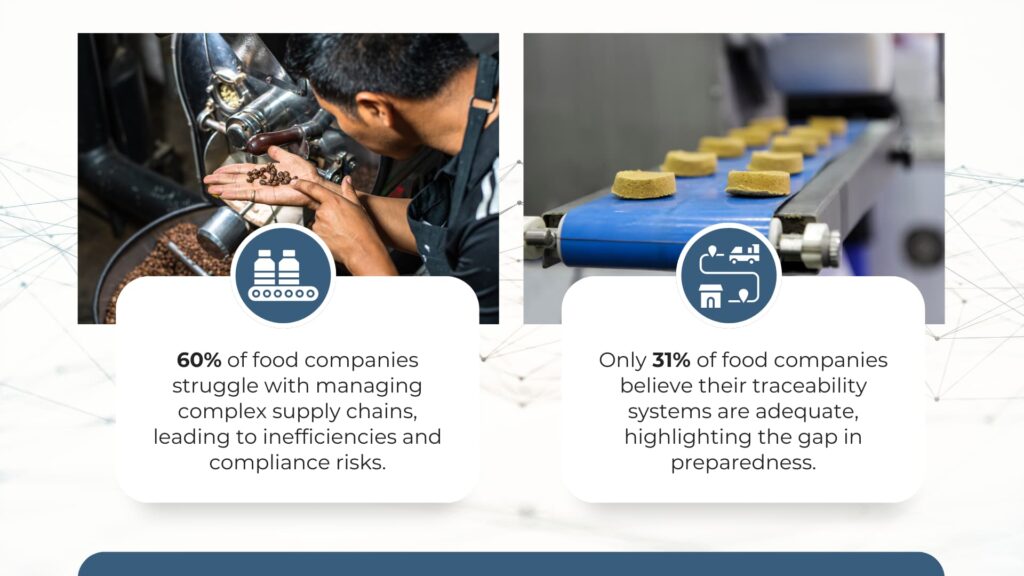
Complying with FSMA 204 is also challenging for food distributors because they deal with multiple suppliers and clients, adding an extra layer of complexity to the traceability process. They must ensure that each step in the distribution chain is meticulously documented, from receiving products to delivering them to the end retailer and food service operator.
A mid-sized distributor managing multiple suppliers without integrated technology might face significant delays in tracking the journey of a product, leading to inaccurate records and potential compliance violations. On the other hand, distributors using automated traceability systems can seamlessly track products from supplier to retailer, ensuring accuracy and compliance.
3. Resource Allocation and Cost Implications
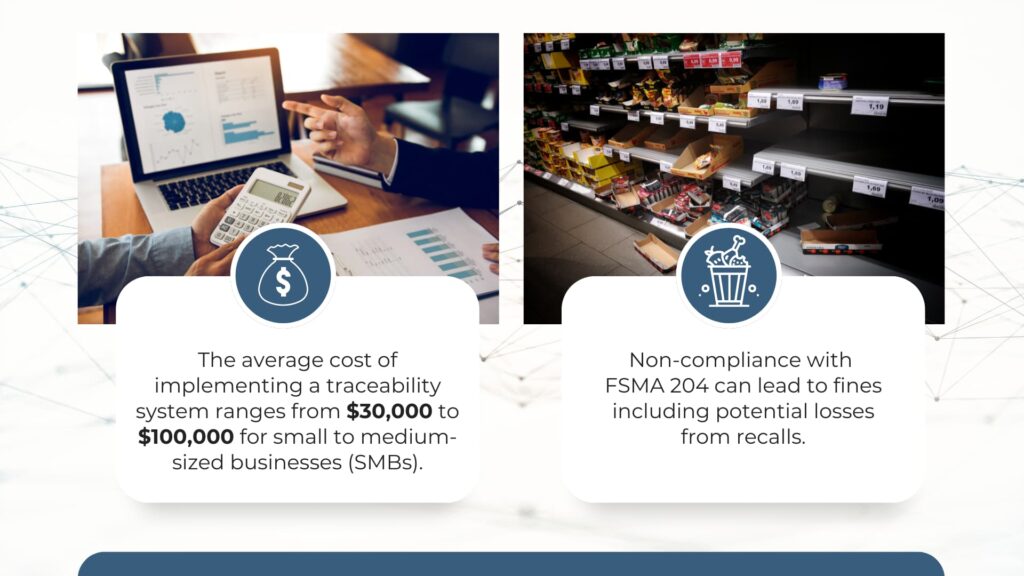
Implementing the required traceability systems can be expensive, particularly for small and medium-sized distributors. The costs associated with upgrading IT systems, training staff, and maintaining accurate records can strain budgets, especially when margins are already tight. However, non-compliance risks—including fines, recalls, and reputational damage—make this investment essential.
A small distributor without a traceability system might initially save costs but face significant financial risk if found non-compliant. Retailers and food service operators, well aware of FDA FSMA Section 204(d), will be demanding their distributor suppliers make these records available to ensure their compliance to the regulation. Investing in a traceability system like Farm To Plate allows the distributor to avoid hefty fines, retain business with current customers, and ensure long-term savings, even though it incurs upfront costs.
4. Leveraging Technology for Compliance
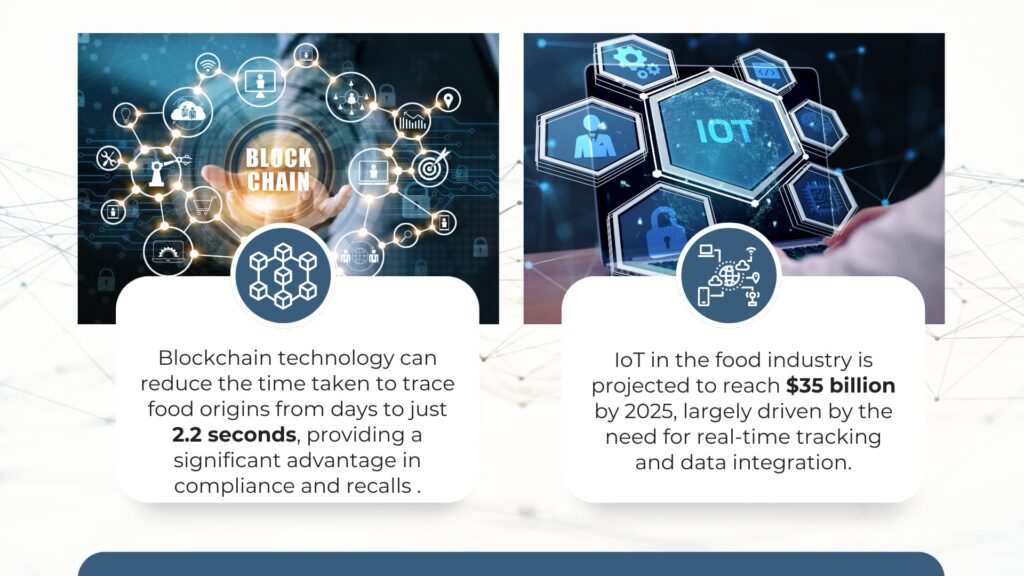
Advanced technologies like Blockchain, AI, barcode scanning, and IoT can play a crucial role in helping distributors comply with FSMA 204. These technologies offer efficient data collection, streamlined recordkeeping, and enhanced traceability, making it easier to meet the FDA’s stringent requirements.
While FDA FSMA Section 204(d) requires a response to a data request within 24 hours in a digital, sortable format, a distributor using manual recordkeeping might take days to trace the source of a contaminated product, whereas a distributor utilizing blockchain technology can do so in seconds. This rapid response time not only ensures compliance but also protects the distributor’s reputation and minimizes the impact of recalls.
5. Collaboration Across the Supply Chain
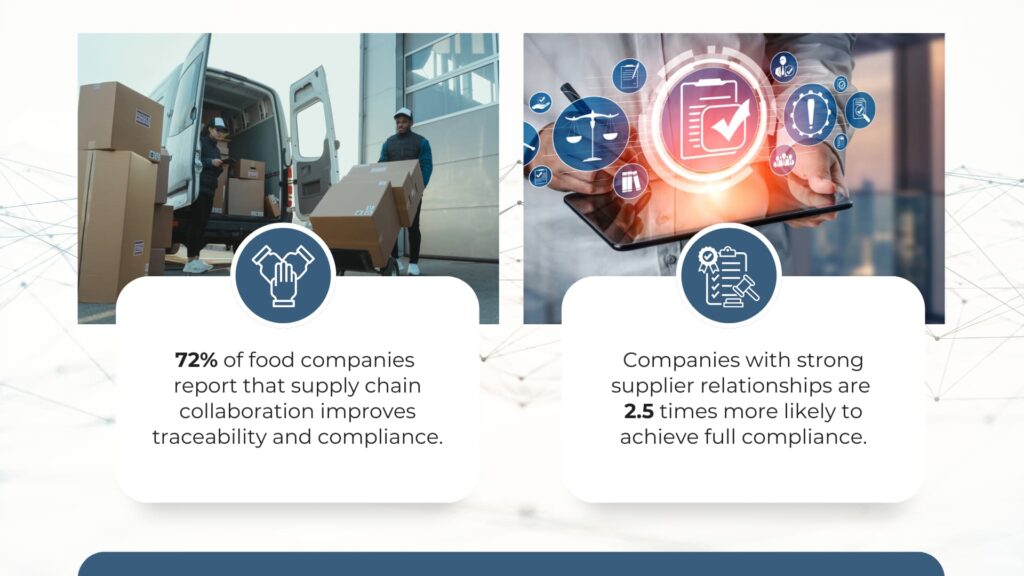
Compliance with FSMA 204 is a collaborative effort. Distributors must work closely with suppliers, and customers to ensure that everyone in the supply chain maintains accurate records and adheres to the same standards. It requires regular communication, data sharing, and coordinated efforts to address any gaps in the traceability process.
Consider a distributor working with multiple suppliers who are not fully compliant with FSMA 204. Without proper collaboration, the distributor risks receiving incomplete or inaccurate traceability data, jeopardizing their compliance status. By fostering strong relationships and regular data sharing with suppliers, the distributor can ensure all parts of the supply chain adhere to FSMA standards.
6. Addressing Product Recalls and Quality Control
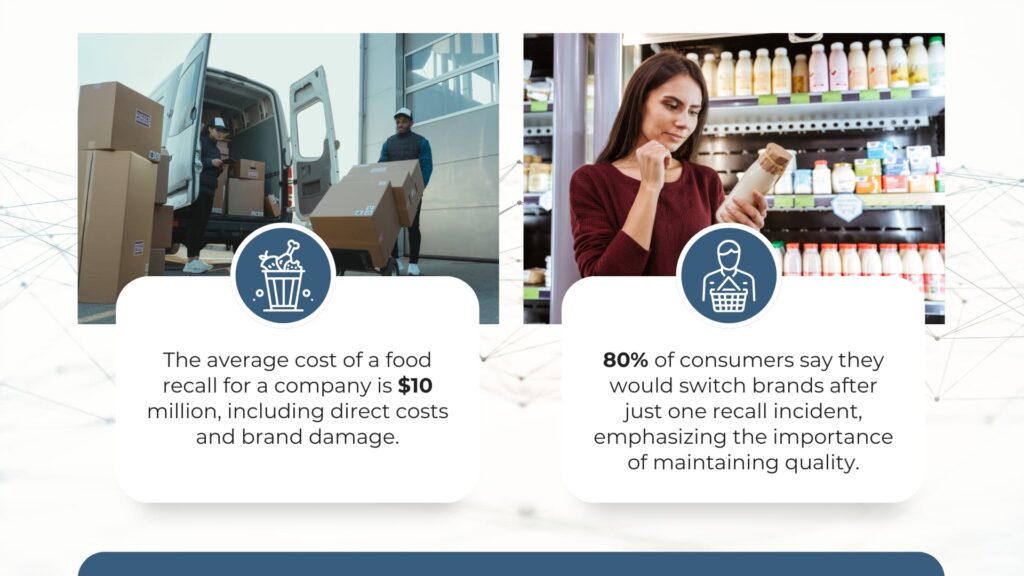
Efficiently managing product recalls requires robust traceability systems. In the event of contamination, distributors must be able to quickly identify affected products and remove them from the supply chain to protect consumers and minimize financial losses.
A distributor without a robust traceability system may face significant delays in identifying and recalling contaminated products, leading to broader public health risks and higher costs. In contrast, a distributor equipped with a strong traceability solution can swiftly execute recalls, minimizing both financial and reputational damage.
7. Preparing for the January 20, 2026 Compliance Deadline
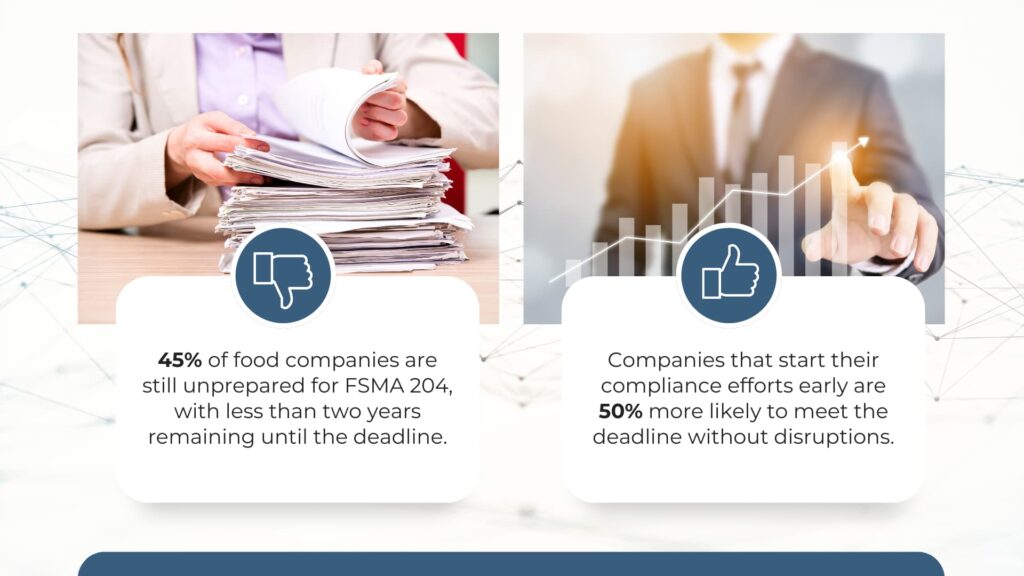
The January 20, 2026, deadline for FSMA 204 compliance is approaching quickly. Distributors must take proactive steps now to ensure they are ready. It includes conducting a thorough gap analysis to identify areas where their current systems may fall short and implementing necessary upgrades or changes well before the deadline.
A distributor that begins compliance preparations early by conducting a thorough gap analysis can identify weaknesses in their current system and address them well before the deadline. In contrast, a distributor that waits until the last minute may struggle with rushed implementations, higher costs, and potential non-compliance.
8. Farm To Plate: Your Partner in Compliance
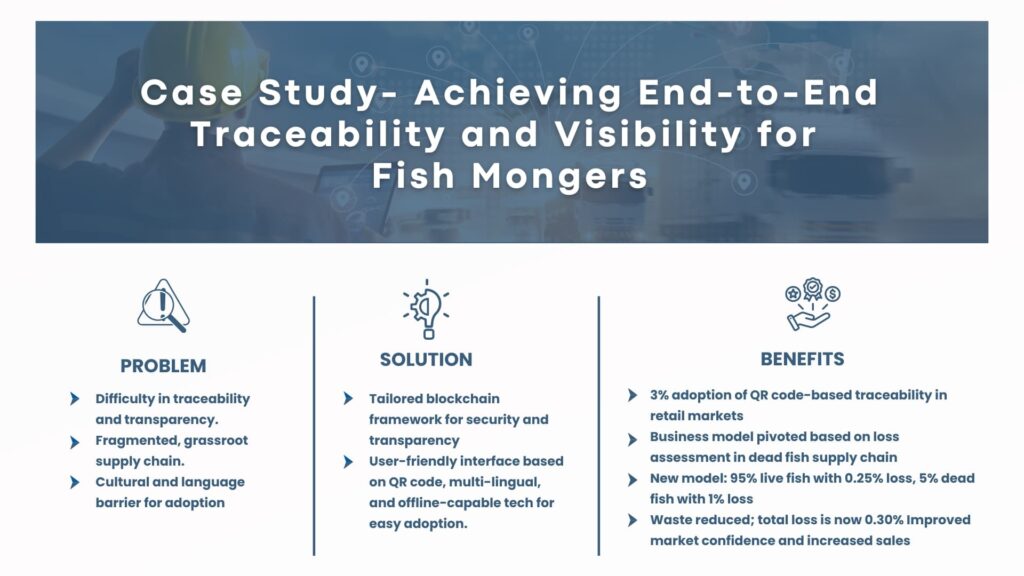
At Farm To Plate, we understand the challenges faced by food distributors. Our platform provides scalable, affordable solutions tailored to your needs. It simplifies compliance by integrating traceability, data management, and supplier coordination. This single, easy-to-use system helps you meet regulatory requirements, maintain operational efficiency, and protect your brand’s reputation.
Our traceability solution seamlessly integrates with your existing systems, ensuring compliance with FSMA 204 while reducing operational costs. With our pay-as-per-use model, you get flexibility without added financial burden, allowing you to navigate supply chains, avoid penalties, and uphold food safety and quality standards.
Namrata Anand, Senior Technical Content Writer at Paramount Software Solutions & farmtoplate.io